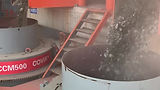
CRUSHER SPECIFICATIONS
Crusher
Specifications
Hydraulic Gyrator Crusher: CCK Series
The CCK Hydraulic Rotary Crusher leverages over 30 years of experience in product design and manufacturing within the crushing industry. Drawing on advanced crusher technology, this efficient hydraulic rotary crusher has been developed to deliver exceptional performance.
The CCK high-efficiency hydraulic rotary crusher combines a high-strength body, advanced hydraulic system, electrical automation, and intelligent control technology. It embodies the latest in rotary crusher technology, surpassing traditional crushers in terms of crushing efficiency, reduced production costs, and ease of maintenance. Its robust design makes it the top choice for efficient coarse crushing in large mining operations.
Features
-
Superior Crushing Capacity: The crusher features a large inclination angle and extended crushing surface, providing powerful crushing force and prolonging liner life.
-
Durable and Reliable Design: A heavy-duty frame, large-diameter integrated spindle, and high-performance bearings ensure enhanced service life and safe, reliable operation. The use of an integral forged spindle eliminates the risks associated with loose moving cones, reducing maintenance needs.
-
Optimised Shaft Strength: The threaded moving cone nut is set on a replaceable alloy steel sheath, preventing stress concentration on the main shaft and enhancing its durability. The upper shaft, with its large diameter and ultra-high strength, is designed to withstand tough and demanding crushing conditions.

CCK Series Technical Parameters
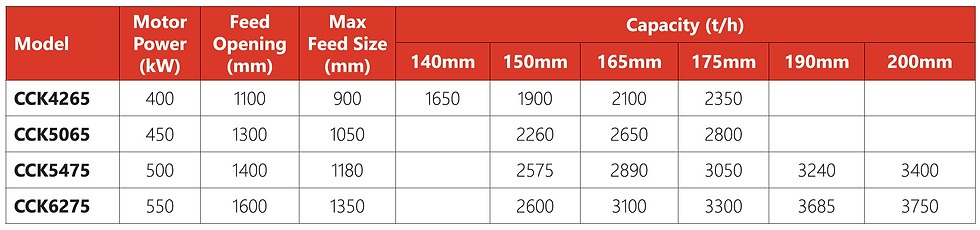
Note: The capacities listed in the table are based on a bulk density of 2.7 t/m³ with smooth and consistent feeding. Smaller settings will yield capacities closer to the lower end, while larger settings will approach the upper range. Actual capacity may vary depending on factors such as feeding method, material characteristics (gradation, moisture content, clay content), bulk density, and crushability.
Jaw Crusher: PJ/PEG Series
The PJ and PEG Series Jaw Crushers are extensively used across industries such as metallurgy, chemicals, construction, power generation, and transportation. Its simple structure, robust build, and reliable performance make it ideal for applications requiring durability, easy maintenance, and low production costs. This crusher is designed to handle various ores and rocks with compressive strengths ranging from 147 to 245 MPa, and can crush materials up to a maximum strength of 320 MPa. Compared to traditional jaw crushers, the PJ series is significantly optimised with a well-designed cavity shape, smoother operation, and reduced energy consumption, making it ideal for coarse crushing of ores and bulk materials.
Features
-
High Strength and Stability: The fully cast body offers exceptional compressive strength, ensuring stable performance with hard materials.
-
Optimised Cavity Design: Enhances throughput by 15-20% while lowering energy consumption.
-
Improved Bearing Lubrication: Enhanced lubrication system reduces bearing temperatures and extends bearing life.
-
Enhanced Crusher Tooth Design: Increases material flow, extending tooth plate lifespan and reducing maintenance costs.
-
Simple and Efficient Maintenance: The straightforward structure allows for quick and easy maintenance, minimising downtime.

PJ Series Technical Parameters

PEG Series Technical Parameters
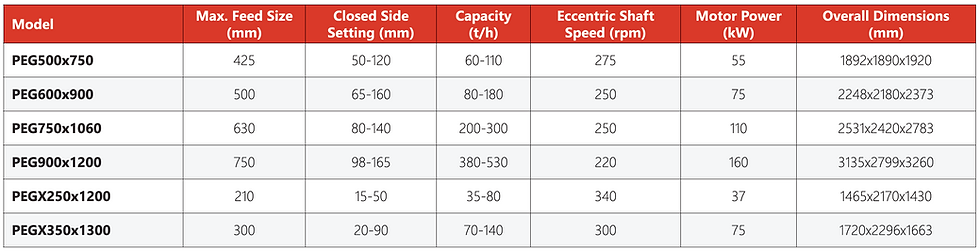
Jaw Crusher: CJ Series
The CJ Series Jaw Crusher features a world-class modular, non-welded main frame structure, ensuring superior reliability and product quality. Upgraded with advanced European technology, it is ideal for primary stage crushing of boulders in industries such as mining, construction, building materials, roads, railways and chemicals.
Features
-
Modular, Non-Welded Structure: The modular design eliminates welding seams, which helps prevent stress concentrations and extends the crusher’s lifespan, particularly under heavy loads.
-
High Capacity: With an optimised cavity shape and discharge opening, the CJ series achieves higher capacity than comparable products. The optimised speed improves movement and performance, resulting in greater throughput.
-
Effortless Installation: The modular main frame simplifies on-site installation and assembly, offering high fatigue resistance and reliability. Its compact design is ideal for sites with limited space or challenging access, such as underground mines or high-altitude locations.
-
Space-Saving Motor Integration: The electric motor is mounted directly on the main frame, reducing the space required for installation and shortening the V-belt length. The motor mount adjusts the belt tension, prolonging its service life and enhancing overall efficiency.
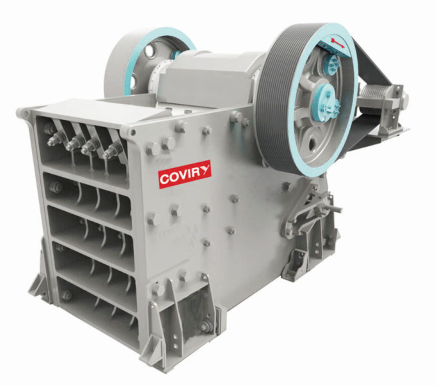
CJ Series Technical Parameters
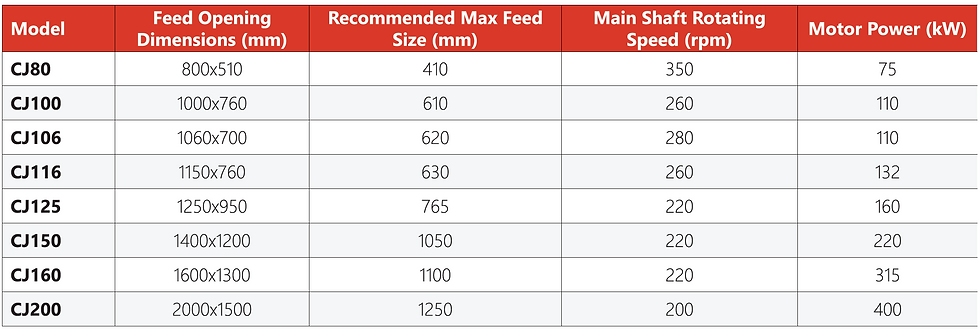
CJ Series Capacity

Hydraulic Cone Crusher: CCH Series
The CCH Series Single-Cylinder Hydraulic Cone Crusher is a high-performance machine designed with advanced international concepts. It features a compact structure, strong crushing force, and excellent efficiency, producing superior product shape. Suitable for secondary and tertiary crushing, it offers multiple cavity options and high reliability. An automated system enhances user-friendliness and simplifies maintenance.
The crusher comes in two variants – CCH and CCHS. The key difference is the feed opening and discharge size, with the CCHS offering a larger capacity. The CCH is ideal for secondary and tertiary crushing, while the CCHS is best for secondary applications.
Working Principle
During operation, the electric motor drives the eccentric via pulleys, V-belts, countershaft, and gears. This causes the main shaft to swing rapidly, making the mantle and concave move toward and away from each other in a periodic motion. Material in the cavity is crushed through continuous squeezing and impact forces. The hydraulic cylinder at the base of the main shaft adjusts its height, allowing for fine control of the closed side setting to produce various product sizes. Multiple cavity configurations and adjustable eccentricity options enable customisation for different output requirements.
Features
-
Versatile Cavity Options: The CCH series offers multiple cavity designs and adjustable eccentricity to suit a wide range of applications and customer needs.
-
High Capacity with Low Operating Costs: Specially designed liners maintain a consistent cavity shape throughout their lifespan, ensuring stable feed size and capacity. This design maximises throughput under similar working conditions and extends liner life, thereby reducing operating costs.
-
Effortless Operation and Maintenance: Maintenance and inspections are performed from above the chamber, simplifying procedures and lowering costs. An advanced sealing system prevents dust entry, prolonging equipment life and minimising upkeep.

CCH Series Technical Parameters

Cavity Description: EC=Extra Coarse, CX= Special Coarse, C= Coarse, MC=Medium, MF=Medium Fine, F=Fine, EF = Extremely Fine, EEF=Extremely Extremely Fine
CCH Series Capacity
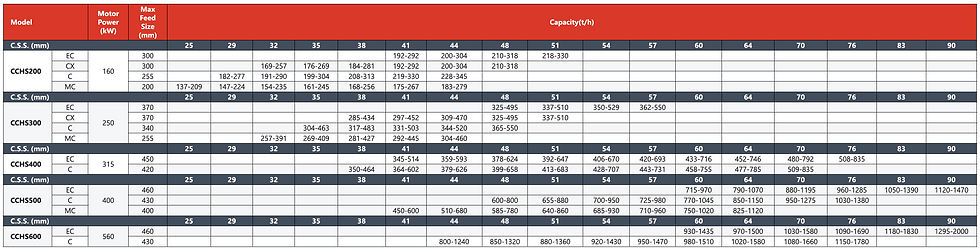
Note: The production capacity table can be used as a tool for the initial modeling of CCH series single red hydraulic circular chain crusher, the data in the table is for the average specific gravity of 2.7t/.m³.
Hydraulic Cone Crusher: CCM Series
The CCM Series Multi-Cylinder Hydraulic Cone Crusher is a world-class, high-performance solution designed for secondary, tertiary, and quaternary crushing. With its unparalleled efficiency and capacity, it excels in handling a wide range of materials, from limestone to basalt, making it ideal for diverse crushing applications.
Working Principle
The CCM series electric motor drives the eccentric via V-belts, countershaft, and gears, causing the mantle to swing with the force generated by the eccentric action. As the mantle moves toward and away from the concave, the material in-between is crushed through compression and impact, then falls to the bottom. The crusher is equipped with hydraulic locking and overload protection systems. If uncrushable material enters the cavity, the hydraulic system automatically releases the pressure to protect the equipment and restores the previous settings after the material passes through, effectively preventing jamming.
Features
-
Robust Structure and Stable Performance: The optimised design ensures high reliability and low operating costs. The inter-particle crushing principle enhances product shape, while the combination of a specialised cavity design and optimised speed increases the proportion of fine products, reducing elongated and flaky particles.
-
Reliable Hydraulic Protection: The hydraulic system for adjustment and overload protection boosts equipment reliability and simplifies maintenance, reducing downtime. Hydraulic cylinders automatically release tramp material that is to hard to be processed in order to prevent jamming, ensuring smooth, continuous operation.
-
Efficient Lubrication for Longevity: The unique oil lubrication system significantly extends equipment lifespan. A high-performance, non-contact labyrinth seal prevents dust ingress and contamination, eliminating issues with oil-water mixing found in traditional spring cone crushers.
-
High Crushing Efficiency and Superior Product Shape: With high speed and large stroke, the CCM series delivers exceptional crushing capacity and efficiency.

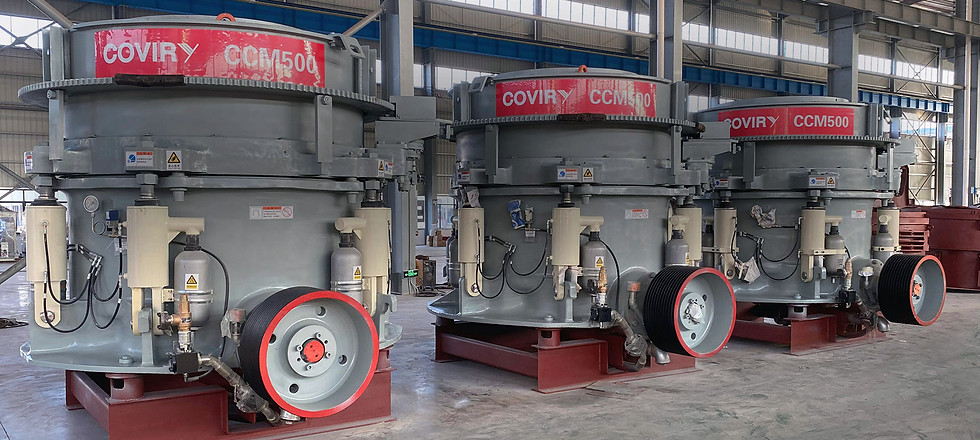
CCM Series Technical Parameters
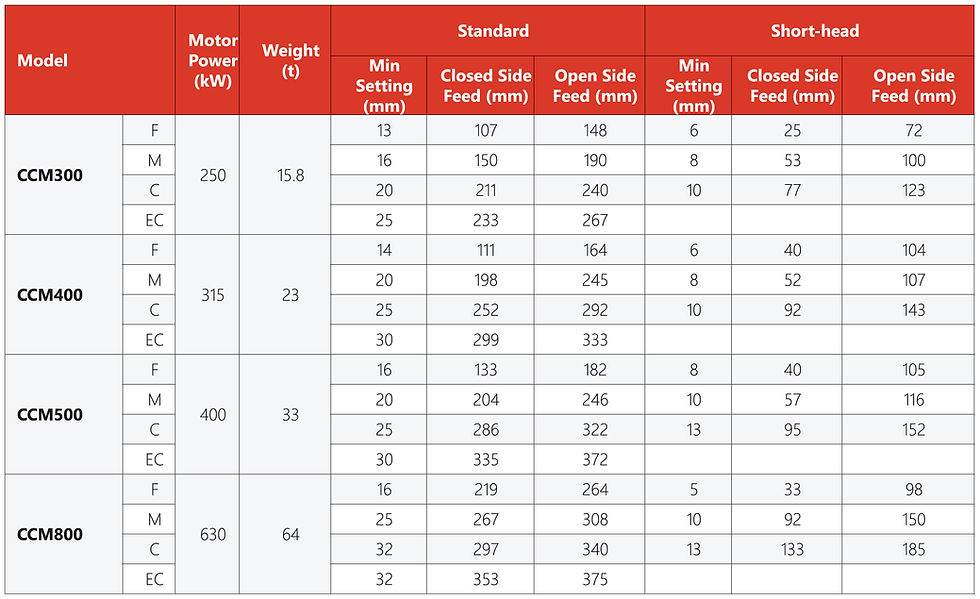
Cavity Description: EC = Extra Coarse, C = Coarse, M = Medium, F = Fine
CCM Series Capacity Under Given Closed Side Settings

Note: The capacity table serves as a preliminary reference for selecting a model from the CCM series multi-cylinder hydraulic cone crushers. The data is based on a material density of 2.7 t/m³ in an open circuit. In a closed circuit with a high percentage of fines in the feed, capacity may increase by 15%-30%. The values provided are nominal peak capacities. For accurate model selection tailored to your specific needs, please consult Coviry Pacific engineers.
CCM 1100 Series
The CCM1100 heavy-duty hydraulic cone crusher combines a compact, robust design with over twice the crushing capacity of similar models. Its features, including a rotatable concave, automatic tramp release, and large feed opening, ensure stable performance and uniform product gradation. The rotatable concave promotes even wear, while the automatic tramp release enables uncrushable materials to pass through seamlessly, maintaining consistent operation and product quality.
CCM 1100 Series Technical Parameters
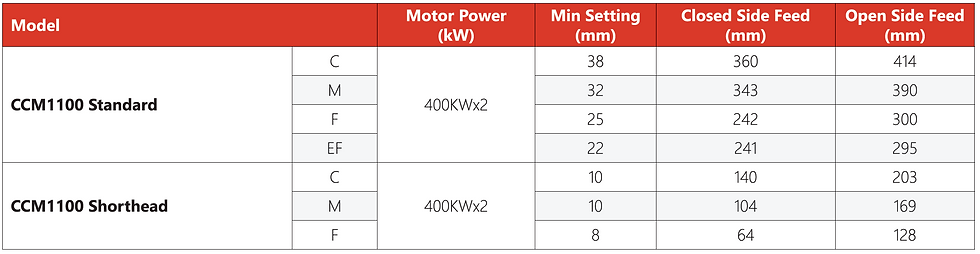
CCM 11100 Series Capacity

Spring Cone Crusher: CCS Series
The CCS Series Spring Cone Crusher is designed on the principles of lamination crushing and a multi-break approach to minimise wear. It combines high swing frequency, optimised cavity design, and efficient stroke to deliver superior performance. Known for its reliability, cost-effectiveness, and robust design, it has gained the trust of users globally as an ideal replacement for traditional cone crushers.
Working Principle
When the crusher is in operation, the motor drives the eccentric via a pulley, countershaft, and gears, causing the main shaft to move in a rapid swinging motion. This motion pushes the mantle and concave closer and apart periodically, crushing the material through continuous squeezing and impact. As the mantle moves away, the crushed material falls through the gap and is discharged from the bottom, allowing only material of the desired size to exit.
Features
-
High Production Efficiency: The combination of high speed and large stroke significantly increases throughput, enhancing the reduction ratio and crushing efficiency.
-
Low Operating Costs: Optimised structural design ensures minimal wear and tear, reducing parts consumption and operating expenses.
-
Reliable Lubrication System: The efficient lubrication system extends equipment life and enhances reliability.
-
Flexible Cavity Options: Easily switch between standard extra-coarse to short-head extra-fine cavities by replacing the mantle and concave, catering to various product size requirements.
-
Ease of Maintenance: All parts can be removed from the top or side, eliminating the need to dismantle the main frame. This design simplifies liner replacement, making routine maintenance quick and efficient.

CCS Series Technical Parameters

Spring Cone Crusher: CCG Series
The CCG Series Spring Cone Crusher is engineered with optimised speed and eccentricity, allowing it to produce finer output with a higher proportion of cubical particles, thanks to its inter-particle crushing principle. The spring-based hydraulic clamping, setting adjustment, and tramp release system simplify operation, making it an ideal choice for conventional crushing plants due to its robust design and ease of maintenance.
Working Principle
The electric motor drives the countershaft via V-belts or couplings, which in turn drives the eccentric using gear and pinion transmission. As the eccentric rotates, the mantle and head assembly move along a conical path. The mantle periodically moves toward the concave, compressing and crushing the material in the cavity. When the mantle retracts, the crushed material is released and discharged. The adjustment ring is secured to the main frame by springs, which absorb excess loads if uncrushable materials enter the cavity. This design prevents damage by increasing the gap between the mantle and concave, allowing uncrushable materials to pass through.
Features
-
Hydraulic System for Easy Adjustment and Tramp Release: Simplifies daily operation and enhances safety.
-
Optimised Cavity Design: Increases throughput by 15-20%, with multiple cavity options for various applications.
-
Effective Grease Sealing: Ensures better sealing and longer service life.
-
Advanced Oil Lubrication Station: Provides reliable lubrication and stability under diverse working conditions.
-
Traditional Structure for Easy Maintenance: Simple design facilitates operation and reduces maintenance efforts.

CCG Series Technical Parameters
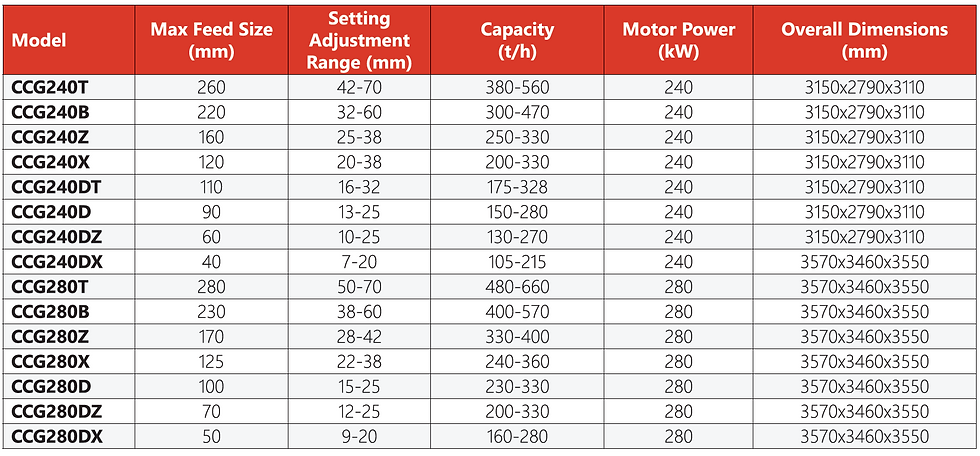
Note: The capacities listed in the table are provided as a preliminary reference for selecting a model from the CCG series cone crushers. The data is based on an average bulk density of 2.7 t/m³ in an open circuit configuration. The capacities represent nominal peak values; actual output may vary depending on factors such as feed gradation, moisture content, clay composition, bulk density, and material crushability.
Vertical Shaft Impact Crusher: CV Series
The CV Series Vertical Shaft Impact Crusher features a specialised rotor design, wear-resistant materials in the crushing cavity, optimised speed, and an advanced hydraulic system. It is extensively used in highways, railways, civil construction, hydropower projects, and concrete mixing, making it the preferred equipment for producing high-quality manufactured sand and aggregate shaping.
Working Principle
Material is continuously fed to the spreader plate at the top of the crusher. Part of the material is directed into the impeller through the feed tube, while the rest overflows through the cascade window. The material entering the impeller is rapidly accelerated and ejected at high speed through the discharge ports, where it collides with cascade material falling from the window (rock-on-rock crushing). The combined materials then hit the liners in the crushing chamber (rock-on-steel crushing) for further reduction. Some material rebounds after colliding with the liners and re-enters the crushing process, undergoing multiple impacts before being discharged from the bottom of the crusher.
Features
-
Sand Making and Aggregate Shaping: Ideal for processing pebbles, limestone, granite, basalt, diabase, and other rocks to produce aggregate chips and sand.
-
Construction Aggregates: Suitable for road pavement, bedding materials, asphalt, concrete, and cement aggregates.
-
Manufactured Sand: Used for shaping aggregates in water conservancy projects, highways, high-speed railways, bridges, airports, and high-rise buildings.
-
Pre-Grinding Crushing: Performs preliminary fine crushing before grinding in mining, and material reduction in industries like construction materials, metallurgy, chemicals, mining, and refractory materials.
-
High-Purity Material Production: Effective for producing glass, quartz sand, and other high-purity materials.

CV Series Technical Parameters

The particle size distribution of finished products is related to the hardness, size and composition of raw materials.
Impact Crusher: CF Series
The CF Series Impact Crusher is a newly developed crusher designed to meet market demands. With a large feed opening, it can crush a wide range of coarse, medium, and fine materials (e.g., granite, limestone, concrete) with compressive strengths up to 350 MPa. It is ideal for applications in highway construction, water conservancy, and power projects. Key features include a high reduction ratio, efficient crushing, production of high-quality cubical-shaped output with no cracks, and ease of maintenance.
Working Principle
The CF series impact crusher operates using impact force. As the rotor spins at high speed, powered by an electric motor, feed materials enter the crushing chamber. The materials first collide with the blow bars on the rotor, then are thrown against the breaker plates. This process repeats as the material bounces back to the blow bars for further impact, passing through multiple crushing zones in the first, second, and third breaker plates. The material is reduced to the desired size through repeated collisions before exiting through the gap between the final breaker plate and the blow bars. Adjusting this gap allows control over the product size and shape.
Features
-
Large Feed Opening & High Crushing Cavity: Handles hard and large-sized materials efficiently.
-
Durable Blow Bars: High-chromium blow bars provide excellent impact and wear resistance.
-
Finished Product Shape: When processing rock with high compressive strengths, the CF Series produces a finished product with a consistent grain shape and a low needle flake rate. Note: Needle flake output also depends on input rock quality and size.
-
Robust Construction: Compact design with a rotor featuring a large moment of inertia.
-
Adjustable Settings: Gap between breaker plates and blow bars can be adjusted to control product size and shape.
-
Versatile Applications: Suitable for both crushing and shaping processes across various industries.


CF Series Technical Parameters

The CF1315Q Impact Crusher is a high-performance machine and features a unique structural design with an extended crushing chamber and a three-stage crushing zone, enhancing both crushing efficiency and production capacity.
Rod Mill: GMB Series
The GMB Series Rod Mill Sand Making Machine, also known as the rod grinding machine, is a high-quality sand-making solution commonly used for processing materials like feldspar, quartz, river pebbles, and granite. The machine is widely applied in sand and stone production, with its rotating cylinder grinding raw materials through impact. As the cylinder rotates, the grinding rods rise to a certain height under friction and centrifugal force, then fall to crush the material, achieving efficient sand production.
Working Principle
The rod mill sand making machine is powered by a motor connected via a reducer and a large gear or directly by a low-speed synchronous motor through the surrounding gear. Inside the rotating cylinder, steel rods act as the grinding medium. Due to centrifugal and frictional forces, the rods are lifted to a certain height before falling back down, crushing the material. Continuous feed enters through the inlet, while ground material is discharged through overflow as new feed is introduced.
Features
-
Wet Sand Process for Environmental Compliance: The wet grinding process reduces dust emissions and meets environmental standards.
-
Efficient Material Processing: The dual-end feed and central discharge design prevent over-crushing, making the equipment compact and efficient.
-
High Capacity and Uniform Output: Ensures consistent particle size and good grading continuity with a large processing capacity.
-
Powerful and Efficient Drive System: Equipped with a synchronous motor (≥400kW) and air clutch combination, optimising power usage.
-
Reduced Power Consumption: Designed to minimise impact on the power grid while maximising sand production, ensuring efficient energy use.

GMB Series Technical Parameters
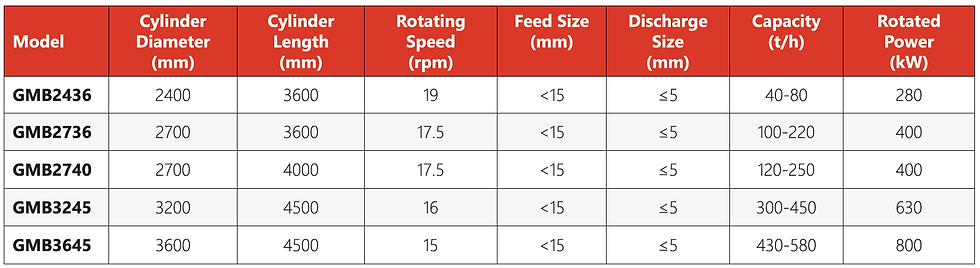